Home / PRECISION CASTING
PRECISION CASTING
PRECISION CASTING
What is precision casting?
Precision castings are known as the highest quality castings available on the market.
Yinxiao can provide brass, steel, aluminum, stainless steel precision casting and precision casting mold services.
Precision casting refers to the general term for the process of obtaining precision-sized castings. Compared with the traditional sand casting process, the castings obtained by precision casting have more precise dimensions and better surface finish. It includes: investment casting, ceramic casting, metal casting, pressure casting, lost foam casting.
Precision casting is also called lost wax casting. Its products are precise, complex and close to the final shape of the parts. They can be used directly without machining or processing, so investment casting is an advanced process of near net formation.

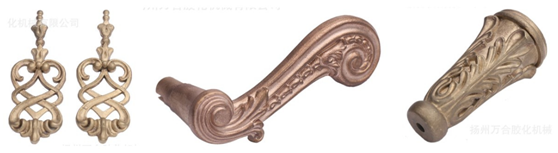
The casting production process is generally so that it can be divided into Pressure wax, making shell, casting, post-treatment, inspection.Pressure wax (Shot wax and making the wax mold)---repair wax----wax inspection----wax tree (wax mold group tree)---shell (dip slurry, sand, dip slurry again, finally Mould shell air-drying)--- dewax (steam dewax)---- bake mold shell --Chemical analysis--casting (casting steel water in the mold shell)----vibration shelling---casting part and pouring Rod cutting separation----grinding sprue---initial inspection (blank inspection)--- ball blast -----cnc machining-----polishing---finish inspection--- entering warehouse.
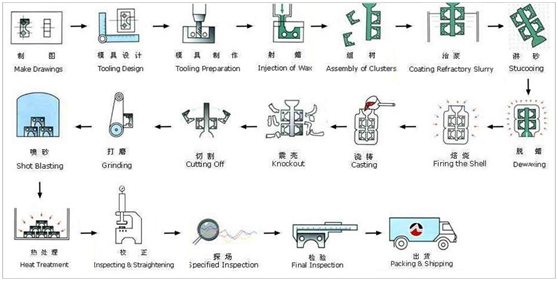
The permeability of the mold shell for investment casting refers to the ability of the gas to pass through the wall of the mold shell, and is an important performance index of the mold shell. The air permeability of the mold shell has a great influence on the molding of the casting. If the permeability of the mold shell is too small, defects such as porosity or insufficient casting may be caused in the casting. In addition, the permeability of the mold shell also has a significant impact on the dewaxing quality of the mold shell.
Factors that affect the casting:
Effect of mold shell permeability on casting quality
1. Under normal circumstances, the molten metal enters the cavity from the sprue cup through the sprue, horizontal runner, and gate. In this process, it is possible that the pouring method is incorrect during the pouring process, resulting in gas entrainment or poor refining of the molten metal itself, or gas generated by the reaction between the molten metal and the refractory impurities of the mold shell. These are the problems often encountered in investment precision casting. Some of these gases can be avoided, and some cannot be avoided. They must have a way out. Either the mold shell or the casting. The mold shell has poor air permeability and gas cannot escape. In the end, the space can only be found from the casting or outside the casting. In the casting, invasive pores are formed; outside the casting, insufficient pouring occurs.
2. When the mold shell is dewaxed, steam is transferred from the outside of the mold shell to the wax mold module. First, the thermal conductivity of the mold shell is better, and secondly, the permeability of the mold shell is also very important. Only in this way, the hot steam can be quickly transferred to the wax mold through the mold shell, and a surface melting layer is formed on the surface of the wax mold instantly, partly penetrates into the mold shell, and partly exits from the gate and runner, otherwise, the wet strength of the mold shell Unable to resist the thermal expansion of the wax mold, which in turn causes cracks in the mold shell and affects the quality of the mold shell and castings.
Factors affecting the permeability of the mold shell
The mold shell is composed of a binder and a refractory material (including powder and pellets), so it has a great relationship with the physical and chemical properties of the binder and the refractory material.
1. Influence of silica sol binder particle diameter on air permeability of mold shell
Because the small colloidal diameter silica sol contains less free water, it can be formulated into a coating with a low powder-liquid ratio. The powder-liquid ratio is low, the coating is not dense, and the air permeability is good. Therefore, in general precision casting manufacturers, the specifications of the silica sol for the front layer and the back layer are inconsistent. The surface layer uses a small colloidal diameter silica sol (typically 8-10nm), while the transition layer and back layer use a large colloidal diameter silica sol (10-20nm).
2.Effect of particle size of refractory on permeability of mold shell
For the surface layer, the transition layer and the back layer, the use of powder and sand with corresponding meshes also has a good effect on the permeability of the mold shell. For example: 300-350 mesh refractory powder is usually used for the surface layer, and 200 mesh refractory powder is used for the transition layer and back layer. In addition, the particle size distribution of sand and powder also has an important effect on the permeability of the mold shell. The sand and powder particle size distribution is too wide and too narrow, which is not good. It is recommended to use sand and powder with bimodal distribution in the data, that is, particle size grading.
3.Effect of coating powder-liquid ratio on the permeability of mold shell
The coating powder-liquid ratio has a greater effect on the permeability of the mold shell. If the viscosity of the coating is high, the powder-liquid ratio will be high, and the coating will be dense, so its permeability will be poor; on the contrary, if the coating viscosity is low, and the powder-liquid ratio is low, the coating will not be dense and the permeability will be improved. Some tests have proved that compared with the coatings with a viscosity of 25s and 40s, the 25s coatings have a 15% lower pouring rate than the 40s coatings.
4.Effect of shell making operation on the permeability of mold shell
Poor operation of the coating process may also cause poor air permeability of the mold shell. For example, if the material is not uniformly controlled when the material is controlled before sanding, which results in local slurry accumulation, it will cause poor air permeability. We often see that there is a thick layer of powder on the part of the mold shell that has been dewaxed. It is very difficult to radiate and exhaust this part of the casting.
5.Effect of Mould Roasting Mould Permeability
The firing of the mold shell greatly affects the air permeability of the mold shell. After the mold shell is fired, the permeability of the mold shell will be greatly improved. Generally, the baking temperature of the silica sol mold shell is 800-1000 ° C. Data show that the temperature of the mold shell is improved. Mainly because the moisture in the mold shell is burned off after firing to leave a certain gap, some small cracks are generated in the mold shell, which causes the mold shell to increase its air permeability. In addition, the firing time is also a determining factor. The length of the firing time determines the degree of firing of the mold shell.
The ways to improve mold shell permeability
1.Correct selection of silica sol
Since the small colloidal diameter silica sol is good for the permeability of the mold shell, it is recommended to use it in the surface layer adhesive. It is best to choose different specifications for the surface layer adhesive and the back layer adhesive.
2. Correctly select the size and size gradation of the refractory
Refractory particle size control is a complex issue. Generally, investment casting manufacturers do not have the capability to conduct inspections, and the inspection costs are not estimated to be low. Therefore, manufacturers should write this content into the purchase agreement when purchasing refractory materials.
3. Formulation of coating powder-liquid ratio
In the case that the strength of the mold shell can be guaranteed, a suitable powder-liquid ratio is used. When the zircon powder is used as the surface layer, the powder-liquid ratio is 3.2-3.4.
4.Effect of shell making operation on the permeability of mold shell
In fact, it is clearly written in the process files and textbooks: the material control must be uniform before hanging sand. The module must be turned continuously to ensure that the slurry is evenly covered on the module, including the final sealing layer. Therefore, as long as the normal operation is strictly in accordance with the process file.
5.Effect of Mould Roasting Mould Permeability
Mold shell firing is mainly for firing. It is necessary to ensure both the baking temperature and the baking time. Generally, the silica sol mold shell has a firing temperature of 800-1000 ° C for at least one hour.
The actual mold case air permeability is a very complicated problem that cannot be completely solved in general factories. When necessary, corresponding measures can be added to strengthen the exhaust through process methods to solve the problem of poor mold case air permeability.
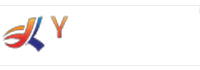
Yinxiao Manufacturing
Quality Service = Quality Products
Navigation
Copyright © 2025 Qingdao Yinxiao Machinery Manufacturing Co., Ltd. Support By BEE Cloud